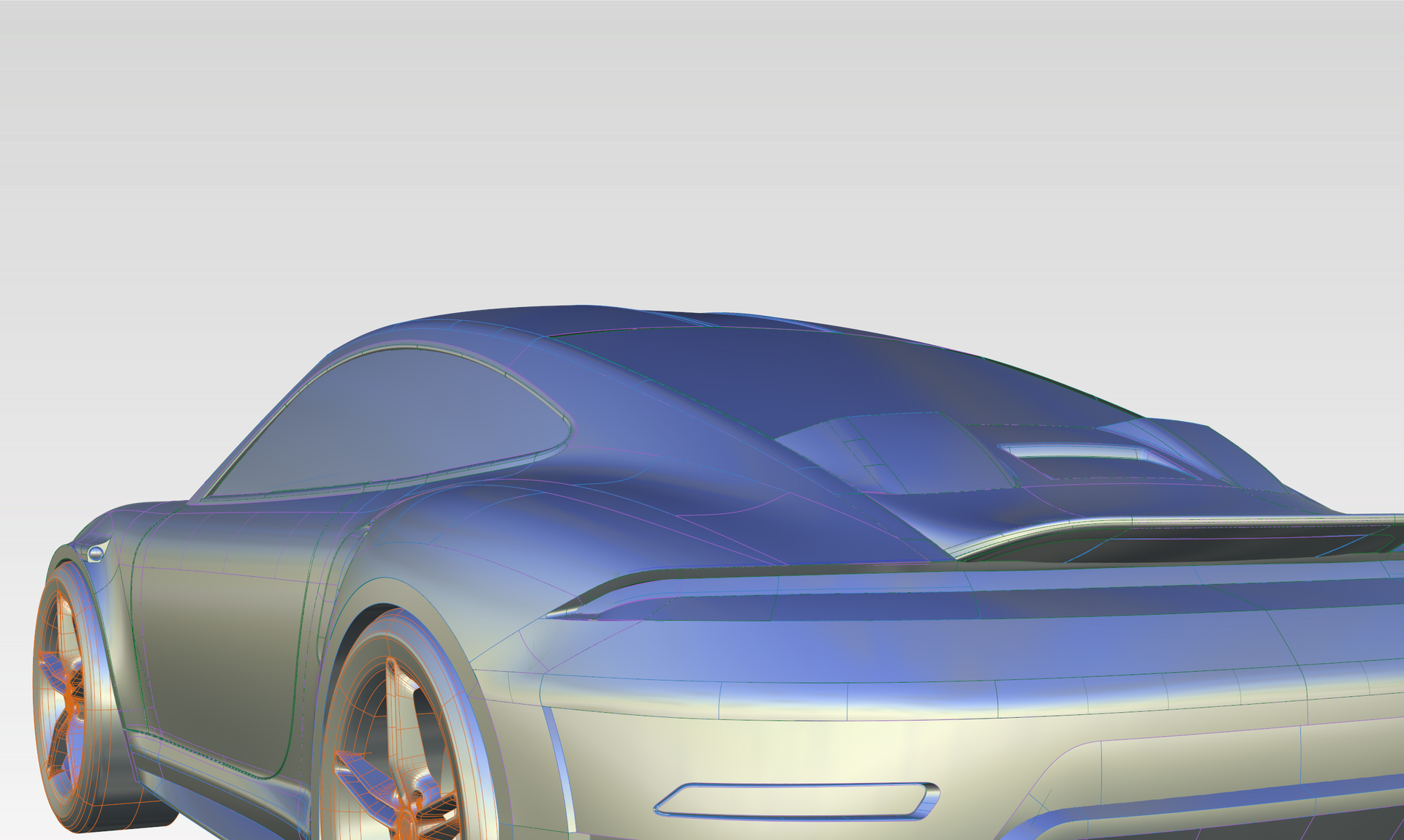
Computer Aided Design Construction
Computer-aided design (CAD), computer-aided styling (CAS), 3D modeling or whatever term you prefer, is traditionally the end result that industrial design or product development ultimately delivers. This includes various phases, from the initial idea to the final product realization.
In my 20 years of experience in the design and automotive industries, I've found that the most effective way to use these tools is to incorporate them early in the ideation phase. Using them as a design aid, similar to sketching in software like Photoshop or Vizcom, allows for quick exploration of shapes and proportions, as well as early identification of potential functional or production issues. These early 3D models serve as a basis for rapid image creation to speed ideation and facilitate communication.
Further along the process, CAD software is used for detailed design, taking into account the initial mass production requirements. Considerations such as draft angles, minimum radii and legal requirements - for example pedestrian protection or the driver's viewing angle - are integrated into the design. In addition, aspects such as assembly, tolerances and heat build-up, such as that encountered in headlights, are carefully considered to ensure optimal fit and function of the final product.
The result of this process is the modelling of the final surfaces of the Class "A" surfaces. These surfaces must meet strict composition, legality and manufacturability requirements while achieving the highest levels of design and surface quality. Collaboration with suppliers is critical at this stage to ensure a seamless integration of design intent and manufacturing capabilities.
An important strategy, as mentioned above, is to start early in the design process, possibly with polygon modeling, which allows for quick and easy changes. We use as few control points as possible and as few as necessary to keep the surface structure simple, which allows for more control and quick and easy changes. This approach to polygon modeling not only facilitates control and quick veining of the shapes, but also the later transition to NURBS modeling, following the principle of "fewer CVs is more". This includes careful construction of the main surfaces at the beginning of the NURBS modeling.
In our Nerbs workflow, we use a point-on-point construction method for our models. This ensures seamless continuity between adjacent surfaces and ensures consistent behavior along edges and clean transitions at radii. In addition, this approach facilitates continuous detailing, especially when collaborating with colleagues who continue to work with these surfaces.
Nerbs modeling
Similarly, the emphasis in NURBS modeling is on using the minimum number of control vertices (CVs) and surfaces required to ensure simplicity, cleanliness, and ease of modification. Surfaces are constructed over carefully defined edges, similar to the principles observed in model building or hand drawing. Careful construction of edges lays the foundation for subsequent surface design, ensuring smooth transitions and precise radius alignment. Considerations such as manufacturing constraints, legal requirements, and assembly aspects are systematically taken into account throughout the development process. Control points are strategically placed on surfaces adjacent to the control points to ensure seamless transitions and precise radius alignment.
Class A Modeling
Tools such as Curvitcher and Enformugs shaders, surface offsets and dimensions are used to ensure compliance with minimum draft radii, clearances and other regulatory standards. Continuous review and refinement ensure that all requirements are carefully met, resulting in a final design that meets both engineering and design criteria and indicates readiness for tool production.
Interested in our services? We’re here to help!
We want to know your needs exactly so that we can provide the perfect solution. Let us know what you want and we’ll do our best to help.